Industry news
Understand thermoplastic dynamic vulcanized rubber (TPV) materials
Release time:2018-12-14 15:10:00
Author:admin
Clicks:
Thermoplastic vulcanizate (English: thermoplastic vulcanizate), abbreviated as TPV, and the Chinese abbreviation of thermoplastic vulcanizate is thermoplastic rubber (English: thermoplastic rubber), abbreviated as TPR, but this name is easily confused with other kinds of thermoplastic elastomers (English: thermoplastic elastomer), because usually thermoplastic elastomers are also known as thermoplastic rubber, especially styrene elastomers, At present, at least in China, "TPR" seems to have become its proprietary name. When TPR is mentioned, it refers to thermoplastic elastomer based on styrene elastomers such as SBS and SEBS, which is inseparable from the large consumption of styrene elastomers in civil and end consumer goods.
If the name of thermoplastic vulcanized rubber is more detailed, it should be thermoplastic dynamic vulcanizate. Adding the word "dynamic" is to more specifically describe the process of producing this thermoplastic vulcanized rubber dynamic vulcanization, which refers to vulcanizing rubber during the melt blending process of rubber and thermoplastic, Of course, rubber is constantly mixed with thermoplastic while vulcanizing, Therefore, the vulcanized rubber is distributed in the thermoplastic continuous phase as a dispersed phase (this structure is very similar to concrete in reality, PP is similar to continuous cement, and rubber particles are similar to small stones in concrete. The corresponding thermoplastic static vulcanized rubber means that the rubber is vulcanized first according to the traditional method, and then the vulcanized rubber is ground into powder through the grinding equipment, and finally blended with molten thermoplastic. In theory, this method can also produce TPV with excellent performance, but so far, only It is in the laboratory stage.
2、 Composition of thermoplastic vulcanized rubber
TPV is mainly composed of two parts, one is plastic as a continuous phase, and the other is rubber as a dispersed phase. Usually rubber needs to be combined with softening oil or plasticizer. Vulcanizing agent and some auxiliary agents are also essential. In addition, some inorganic fillers will be added in order to reduce costs or improve some aspects of performance.
TPV can be formed between many plastics and rubbers, but only a few blends have practical value after dynamic vulcanization. Currently, there are PP / PE / EPDM, PP / NBR, PA6 / ACM, PP / SEBS, TPEE / AEM commercialized. In the book thermoplastic elastomer published by Chemical Industry Press, 99 Kinds of rubber / plastic blends prepared from 11 kinds of rubber and 9 kinds of plastics were reviewed. It was found that the following conditions must be met in order to obtain the best rubber / thermoplastic dynamic vulcanization Blend: (1) the surface energy of the two polymers of plastic and rubber is matched; (2) The molecular chain length of rubber entanglement is low; (3) The crystallinity of the plastic is more than 15%. When the polarity or surface energy difference between plastic and rubber is relatively large, the blend with excellent performance can also be obtained by adding a suitable compatibilizer and then conducting dynamic vulcanization.
3、 Preparation of thermoplastic vulcanized rubber
There are three kinds of preparation methods of TPV, namely melt blending, solution blending and latex blending. Among them, melt blending is the most common method, and there are mainly two kinds of equipment, mixer or twin-screw extruder. Depending on the process, one type of equipment can be used alone or both. In industry, due to the continuous production of twin-screw extruder, considering the stable quality, twin-screw extruder has become the most common dynamic vulcanization equipment.
The specific steps of dynamic vulcanization are as follows: first, melt and blend rubber and plastic in an internal mixer. When they are fully mixed, add vulcanizing agent. At this time, mix and vulcanize. If the vulcanization speed is faster, the mixing degree must be more intense to ensure that the blend has good processing performance. At present, because there are granular rubber for sale, plastic and rubber can be mixed directly by twin-screw extruder without internal mixer. In the specific process, dynamic vulcanization can be carried out in two steps, and plastics can be added and mixed with rubber in two times to protect plastics from the oxidation of vulcanizing agent during dynamic vulcanization.
4、 Properties and characteristics of thermoplastic vulcanized rubber
The properties and characteristics of TPV are mainly determined by its composition, and the dynamic vulcanization process also has a great impact on it.
In terms of composition and technology, TPV is vulcanized rubber powder dispersed in the plastic phase, so it is closer to traditional rubber in performance, with high temperature resistance, low compression deformation, solvent resistance, oil resistance, etc. Although other thermoplastic elastomers can maintain good mechanical properties at room temperature and even exceed TPV, once the temperature rises, the mechanical properties will decrease rapidly!
In terms of processing, TPV can be processed on conventional plastic injection molding machines, extruders and blow molding machines, reflecting the processing advantages of thermoplastics. It can produce products in the fastest speed and in large quantities, so as to reduce the excessive investment of equipment and manpower by manufacturers, and greatly change the excessive use of energy and environmental protection!
At present, the TPV that has been commercialized and used in batches mainly takes EPDM as the dispersed phase, and the continuous phase is usually pp. if classified by the vulcanization system, the TPV that is vulcanized by phenolic resin and peroxide is more mature at present: generally, the TPV that is vulcanized by phenolic resin has better high temperature resistance and climate resistance; In addition, for blow molding, phenolic resin vulcanized TPV is more suitable, while peroxide vulcanized TPV can achieve a more delicate surface, a slightly lower processing temperature, better coloring, and lower moisture absorption than phenolic resin.
5、 Application and market of thermoplastic vulcanized rubber
Because TPV is closer to traditional rubber in terms of high temperature resistance, oil resistance and solvent resistance, its application is more in the field of industrial products, but its performance still lags behind that of traditional rubber, so it can not completely replace rubber in fields requiring high mechanical properties, oil resistance and high temperature resistance.
At present, TPV based on PP / EPDM is mainly applied in the following aspects:
(1) In the field of building sealing strips: it usually replaces the traditional EPDM rubber. Because of its advantages in weather resistance, EPDM is generally used in building industry sealing strips. In addition, TPV is easy to process, so since the birth of TPV, the building industry has been an important market of TPV;
(2) In the field of automotive sealing products: with the consideration of light weight and environmental friendliness of automobiles, TPV has replaced more traditional EPDM and NBR, and is widely used in window sealing strips, triangle windows, glass guide grooves, front and rear windshield glass wrapping;
(3) Wire and cable field: TPV is usually used for the cable sheath layer used outdoors and requiring flexibility, and most of the sheath or insulation layer of general automobile ignition wires are TPV;
(4) Railway rail insulation cushion pad: in general, traditional rubber can also be used, but the short-term large-scale supply of railway projects causes the traditional rubber production method to lag behind the schedule. The use of TPV can meet the requirements of fast large-scale supply;
(5) Other hardware tool handles, sealing rings, gaskets, etc.: generally, products in this field can also use Styrene Elastomer (TPR), but when it needs to have certain high temperature resistance, oil resistance or solvent resistance, TPV will be considered more.
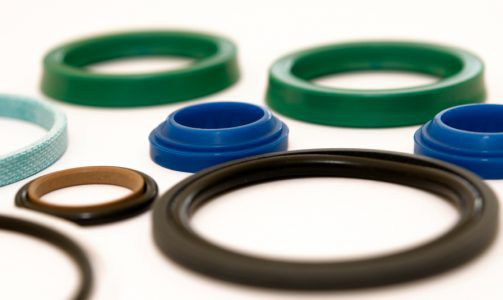
If the name of thermoplastic vulcanized rubber is more detailed, it should be thermoplastic dynamic vulcanizate. Adding the word "dynamic" is to more specifically describe the process of producing this thermoplastic vulcanized rubber dynamic vulcanization, which refers to vulcanizing rubber during the melt blending process of rubber and thermoplastic, Of course, rubber is constantly mixed with thermoplastic while vulcanizing, Therefore, the vulcanized rubber is distributed in the thermoplastic continuous phase as a dispersed phase (this structure is very similar to concrete in reality, PP is similar to continuous cement, and rubber particles are similar to small stones in concrete. The corresponding thermoplastic static vulcanized rubber means that the rubber is vulcanized first according to the traditional method, and then the vulcanized rubber is ground into powder through the grinding equipment, and finally blended with molten thermoplastic. In theory, this method can also produce TPV with excellent performance, but so far, only It is in the laboratory stage.
2、 Composition of thermoplastic vulcanized rubber
TPV is mainly composed of two parts, one is plastic as a continuous phase, and the other is rubber as a dispersed phase. Usually rubber needs to be combined with softening oil or plasticizer. Vulcanizing agent and some auxiliary agents are also essential. In addition, some inorganic fillers will be added in order to reduce costs or improve some aspects of performance.
TPV can be formed between many plastics and rubbers, but only a few blends have practical value after dynamic vulcanization. Currently, there are PP / PE / EPDM, PP / NBR, PA6 / ACM, PP / SEBS, TPEE / AEM commercialized. In the book thermoplastic elastomer published by Chemical Industry Press, 99 Kinds of rubber / plastic blends prepared from 11 kinds of rubber and 9 kinds of plastics were reviewed. It was found that the following conditions must be met in order to obtain the best rubber / thermoplastic dynamic vulcanization Blend: (1) the surface energy of the two polymers of plastic and rubber is matched; (2) The molecular chain length of rubber entanglement is low; (3) The crystallinity of the plastic is more than 15%. When the polarity or surface energy difference between plastic and rubber is relatively large, the blend with excellent performance can also be obtained by adding a suitable compatibilizer and then conducting dynamic vulcanization.
3、 Preparation of thermoplastic vulcanized rubber
There are three kinds of preparation methods of TPV, namely melt blending, solution blending and latex blending. Among them, melt blending is the most common method, and there are mainly two kinds of equipment, mixer or twin-screw extruder. Depending on the process, one type of equipment can be used alone or both. In industry, due to the continuous production of twin-screw extruder, considering the stable quality, twin-screw extruder has become the most common dynamic vulcanization equipment.
The specific steps of dynamic vulcanization are as follows: first, melt and blend rubber and plastic in an internal mixer. When they are fully mixed, add vulcanizing agent. At this time, mix and vulcanize. If the vulcanization speed is faster, the mixing degree must be more intense to ensure that the blend has good processing performance. At present, because there are granular rubber for sale, plastic and rubber can be mixed directly by twin-screw extruder without internal mixer. In the specific process, dynamic vulcanization can be carried out in two steps, and plastics can be added and mixed with rubber in two times to protect plastics from the oxidation of vulcanizing agent during dynamic vulcanization.
4、 Properties and characteristics of thermoplastic vulcanized rubber
The properties and characteristics of TPV are mainly determined by its composition, and the dynamic vulcanization process also has a great impact on it.
In terms of composition and technology, TPV is vulcanized rubber powder dispersed in the plastic phase, so it is closer to traditional rubber in performance, with high temperature resistance, low compression deformation, solvent resistance, oil resistance, etc. Although other thermoplastic elastomers can maintain good mechanical properties at room temperature and even exceed TPV, once the temperature rises, the mechanical properties will decrease rapidly!
In terms of processing, TPV can be processed on conventional plastic injection molding machines, extruders and blow molding machines, reflecting the processing advantages of thermoplastics. It can produce products in the fastest speed and in large quantities, so as to reduce the excessive investment of equipment and manpower by manufacturers, and greatly change the excessive use of energy and environmental protection!
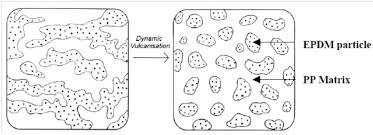
At present, the TPV that has been commercialized and used in batches mainly takes EPDM as the dispersed phase, and the continuous phase is usually pp. if classified by the vulcanization system, the TPV that is vulcanized by phenolic resin and peroxide is more mature at present: generally, the TPV that is vulcanized by phenolic resin has better high temperature resistance and climate resistance; In addition, for blow molding, phenolic resin vulcanized TPV is more suitable, while peroxide vulcanized TPV can achieve a more delicate surface, a slightly lower processing temperature, better coloring, and lower moisture absorption than phenolic resin.
5、 Application and market of thermoplastic vulcanized rubber
Because TPV is closer to traditional rubber in terms of high temperature resistance, oil resistance and solvent resistance, its application is more in the field of industrial products, but its performance still lags behind that of traditional rubber, so it can not completely replace rubber in fields requiring high mechanical properties, oil resistance and high temperature resistance.
At present, TPV based on PP / EPDM is mainly applied in the following aspects:
(1) In the field of building sealing strips: it usually replaces the traditional EPDM rubber. Because of its advantages in weather resistance, EPDM is generally used in building industry sealing strips. In addition, TPV is easy to process, so since the birth of TPV, the building industry has been an important market of TPV;
(2) In the field of automotive sealing products: with the consideration of light weight and environmental friendliness of automobiles, TPV has replaced more traditional EPDM and NBR, and is widely used in window sealing strips, triangle windows, glass guide grooves, front and rear windshield glass wrapping;
(3) Wire and cable field: TPV is usually used for the cable sheath layer used outdoors and requiring flexibility, and most of the sheath or insulation layer of general automobile ignition wires are TPV;
(4) Railway rail insulation cushion pad: in general, traditional rubber can also be used, but the short-term large-scale supply of railway projects causes the traditional rubber production method to lag behind the schedule. The use of TPV can meet the requirements of fast large-scale supply;
(5) Other hardware tool handles, sealing rings, gaskets, etc.: generally, products in this field can also use Styrene Elastomer (TPR), but when it needs to have certain high temperature resistance, oil resistance or solvent resistance, TPV will be considered more.